A multimeter is arguably the most important tool an electrician has in their toolbelt and the first thing most reach for in the beginning phases of troubleshooting. When identifying issues with rotary encoders in conveyor systems, the multimeter can help detect a range of problems before turning to more specialized equipment.
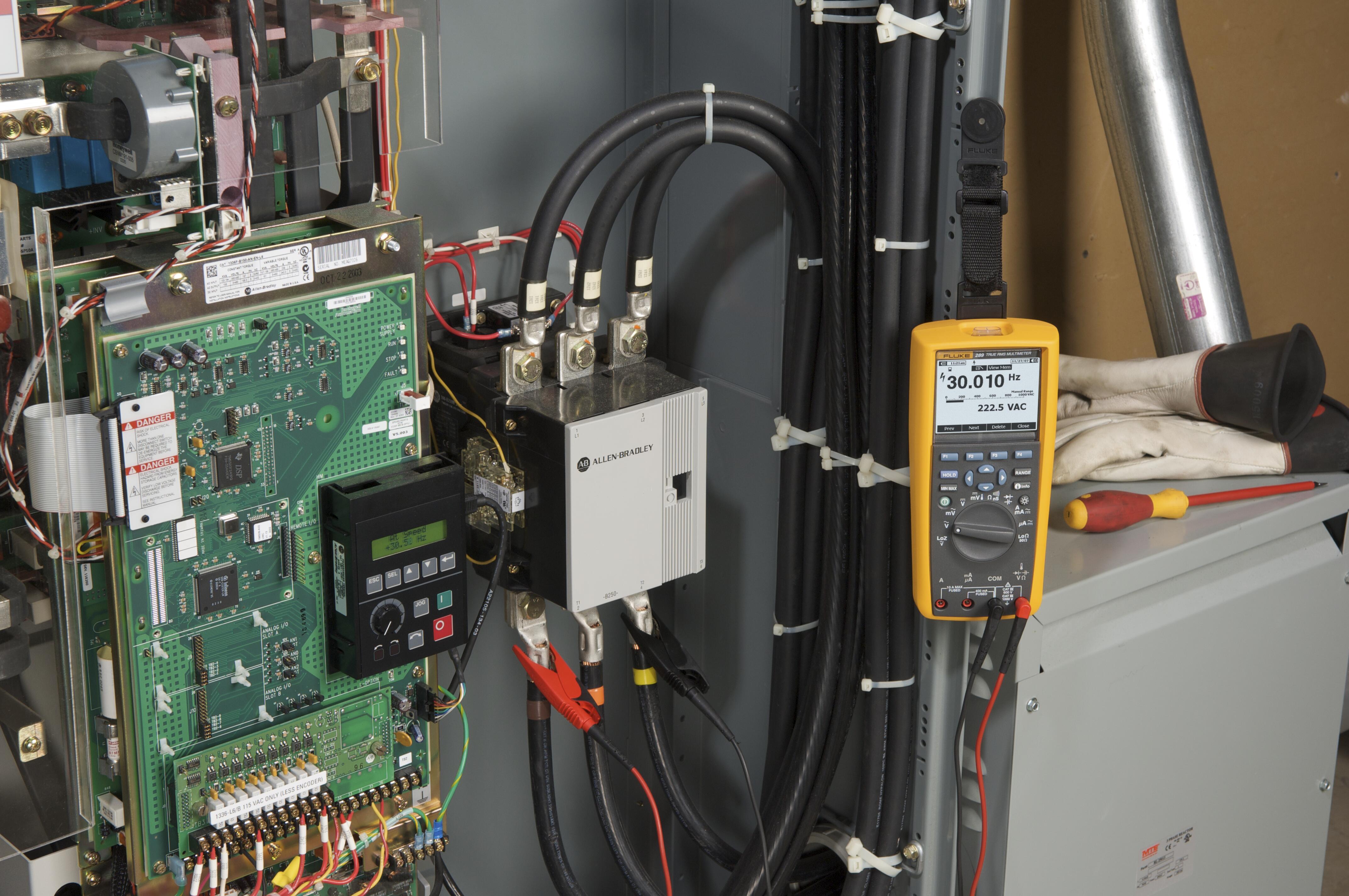
In this article, we’ll discuss how to use a multimeter to troubleshoot rotary encoders and walk through step-by-step instructions.
Understanding Rotary Encoders
A rotary encoder converts the position of a rotating shaft into a digital signal. In a conveyor system, they monitor and control the progression of the conveyor and provide feedback. This allows precise timing for other actions on the system, such as cutting a precise length of packing tape, removing products that don’t meet weight specifications, or moving products from one assembly line to another.
Without the precise information provided by rotary encoders, many conveyor systems wouldn’t be able to fully function. When encoders are moving the conveyor system erratically or providing inaccurate information to other systems, production comes to a halt. Fixing issues is paramount to getting the system back up and running.
Using a Digital Multimeter to Troubleshoot Rotary Encoders
While the problem may appear to be within the rotary encoder, perform a visual inspection for obvious signs of damage to wiring or loose connections first. If that doesn’t solve the issue, here’s how to use a digital multimeter to help identify the problem.
1.?? Safety Precautions
Before proceeding with any electrical measurements, ensure that you follow these safety precautions:
●????? Wear personal protective equipment (PPE): Always wear insulated gloves, safety glasses, and any other required PPE to protect against electrical shock and arc flash. Consult the National Fire Protection Association (NFPA) 70E standard to ensure that you are wearing the right PPE for the environment you are testing in.
●????? Check multimeter ratings: Ensure your digital multimeter is rated for the voltage and current levels present in the circuit. It should also be properly rated for the environment (e.g., CAT III or CAT IV for industrial applications).
●????? Inspect test leads: Make sure the test leads are in good condition, with no exposed wires or damage. Test leads should also be rated for the voltage level you are working with.
●????? Check resistance of test leads: Insert leads in the volt/ohms (VΩ) and COM inputs. Set your meter to measure ohms and touch the probe tips together. Good leads will measure 0.1 to 0.3 ohms.
2.?? Measure the Voltage
●????? Select the correct measurement mode: Set the multimeter to DC voltage mode (V with a dotted line and a solid line over it, V?).
●????? Select the voltage range: If your multimeter does not automatically select the range, set it to a range higher than the expected voltage. If you are not sure what the expected voltage is, choose the highest range setting on the multimeter.
●????? Connect the test leads: Insert the black probe into the COM port and the red probe into the VΩ port.
●????? Connect the probes: Connect the black probe to ground. Connect the red probe to the signal output (A, B, and Z or index channel if available).
●????? Read the results: Measure the average voltage. Then, use the Peak Min/Max function to check the peak voltage.
Figure 1. Digital multimeter displaying the rotary encoder's average (2.477 V) and peak (4.869 V) voltages. These readings are within normal range.
●????? Repeat: Repeat with other channels until you have readings for each one.
●????? Interpret the results: If the readings are higher or lower than expected, as specified in the manufacturer’s encoder datasheet, it could indicate a few different issues. These could be electrical, mechanical, or even environmental issues. Here are a few examples:
a.???? Power supply problems — If the power supply voltage is too high or too low, it can affect the output signals of the encoder.
b.???? Signal wiring or connection issues — Faulty or loose wiring, poor connections, or incorrect wiring can cause incorrect voltage readings on the encoder’s output channels.
c.???? Electrical noise or interference — Electrical noise from nearby equipment or improper grounding can cause interference, leading to incorrect voltage readings.
d.???? Encoder signal loading or impedance mismatch — If the circuit that the encoder is connected to has an impedance mismatch or too much load, it can affect the signal voltage levels.
3.?? Measure the Frequency
Using the same methods noted above, measure the rotary encoder’s frequency (Hz):
○????? Select the Hz function on the multimeter.
○????? Ensure the red probe is inserted into the Hz or VΩ port, depending on your multimeter model.
○????? Connect the black probe to ground and the red probe to the A channel output wire.
○????? Test the frequency of the A channel.
○????? Repeat with the B channel and Z channel, if available.
○????? Interpret the results: The frequency of the A channel should match the encoder specifications. The frequency of the B channel should be the same as the frequency of the A channel. If a Z channel is present, the frequency should correspond to one pulse per revolution of the rotary encoder.
○????? If the resulting frequencies are outside of expected parameters, it could indicate a few different problems:
■????? Mechanical issues — Slippage, wear, or improper installation can cause incorrect rotation speeds or irregular pulses.
■????? Electrical noise or interference — Noise from nearby equipment or improper grounding can affect signal quality and result in incorrect frequency readings.
■????? Wiring issues — Poor connections, broken wires, or incorrect wiring can lead to signal loss or incorrect pulses.
■????? Encoder malfunction — Internal encoder faults, such as worn-out components or sensor failure, can cause incorrect frequency output.
4.?? Measure the Duty Cycle
Using the same methods noted above, measure the rotary encoder’s duty cycle (%):
○????? Select the duty cycle (%) function on the multimeter.
○????? Ensure the red probe is inserted into the VΩ port and the black probe in the COM port.
○????? Connect the black probe to ground and the red probe to the A channel output wire.
○????? Test the duty cycle of the A channel.
○????? Repeat with the B channel and Z channel, if available.
○????? Interpret the results: The A and B channels should both show results close to 50%. The Z channel, if available, will show a much lower duty cycle since it only pulses one time per revolution.
○????? If the resulting duty cycles are outside of expected parameters, it could indicate a few possible problems:
■????? Encoder misalignment or mechanical issues — Misalignment can cause irregular pulses, resulting in a duty cycle that is too high or too low, depending on how the sensors interpret the disk movement.
■????? Electrical noise or interference — Noise can create false pulses or alter the duration of the high and low states, causing the duty cycle to deviate from its normal value.
■????? Signal degradation or weak signal — Degraded signals may not switch cleanly between high and low states, causing a duty cycle that is inconsistent or outside expected parameters.
■????? Faulty or worn-out encoder components — A worn-out or dirty encoder disk may not properly interrupt the light path in optical encoders, leading to incorrect signal timing and an abnormal duty cycle.
Figure 2. Digital multimeter displaying the rotary encoder's frequency (52.5 Hz) and duty cycle (50%)
In the example above, the digital multimeter displays results within the normal ranges.
Limitations of a Digital Multimeter in Troubleshooting a Rotary Encoder
The rotary encoder may be experiencing issues that are simply not detectable with a multimeter. For example, the A and B channels may be out of phase. While each one may be operating correctly on its own, the multimeter is unable to tell if they are incorrectly phased relative to each other.
Because none of the measurements that you can take with a multimeter reveal a problem, it's time to consider a tool that gives more information, such as a handheld oscilloscope.
Conclusion
Digital multimeters can help identify some of the problems a rotary encoder may be experiencing. However, a handheld oscilloscope is needed for a more in-depth analysis. Since it displays a picture of the waveforms, it can help you identify issues like noise, timing issues, or other issues in the waveforms. With this information, you’ll be better equipped to identify the source of the problem with the rotary encoder.
?
?
?